Sustainability
Our core mission is to invest in the development of the energy supply essential to human and economic progress, while effectively managing social and environmental concerns, including climate change.
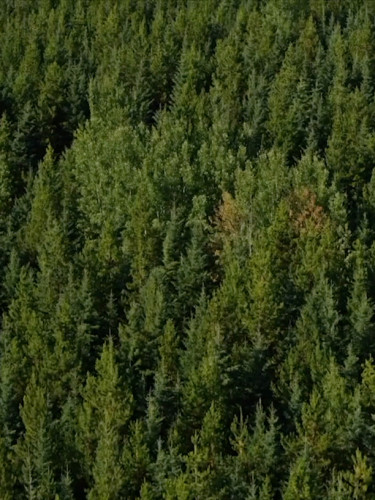
-
Integrating sustainability
Comprehensive governance and risk management. -
Managing climate-related risks
Resilient strategy for the energy transition. -
Managing nature-related risks and impacts
-
Social
Strengthening communities. -
Performance metrics
Measuring and monitoring performance. -
Low carbon technologies
Managing energy transition opportunities
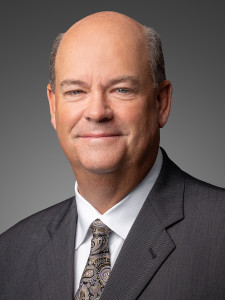
A message from Ryan Lance, Chairman and CEO
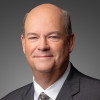
Key Milestones
We have a long standing, risk-based approach to sustainable development.
2023
- Achieved OGMP 2.0 Gold Standard Pathway
2022
-
Strengthened GHG target to 50-60% intensity reduction on operated and equity basis by 2030
-
Set goal for near zero methane emissions intensity by 2030
- Published Plan for Net-Zero Energy Transition
2021
-
Strengthened GHG target to 40-50% intensity reduction on operated and equity basis by 2030
- Established Low Carbon Technologies organization
2020
- Set net-zero ambition
-
Established GHG target of 35-45% intensity reduction for operational emissions by 2030
-
Committed to zero routine flaring by 2030 with ambition to achieve by 2025
2010-2019
-
Established climate risk and biodiversity strategies
- Integrated sustainability into enterprise risk management process
-
Set long term GHG reduction target
2000-2009
-
Adopted public positions on SD, climate, biodiversity, water and human rights
-
Published first SD report
-
Developed Climate Change Action Plan
2024 Sustainability Report
Our work in 2024 included projects that minimized environmental risk and impact, while benefiting communities.
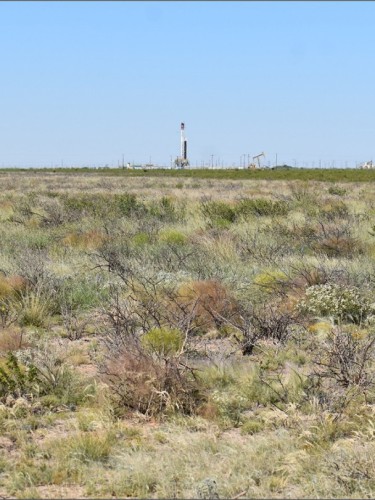
Sustainability news
Spotlight stories about how we are managing sustainability risks.
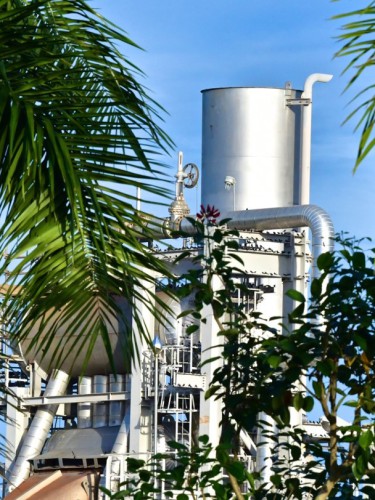
-
Sustainable Development Position
We have a long-standing position on sustainable development.
-
Custom Sustainability Report Builder
Download the entire report or specific sections.
Sustainability projects
We deliver reliable and affordable energy to the world while protecting the environment and benefiting communities. This interactive map provides examples of our efforts across the globe.