ConocoPhillips has the technical capability to operate globally while maintaining a relentless focus on safety and environmental stewardship. We manage our operations through six operating segments defined by geographic area: Lower 48; Europe, Middle East and North Africa; Asia Pacific; Alaska; Canada; and Other International. ConocoPhillips’ operating segments include a strong base of legacy production, multiple ongoing development programs that offer low cost of supply and low carbon intensity, along with focused exploration opportunities.
Exploration and production
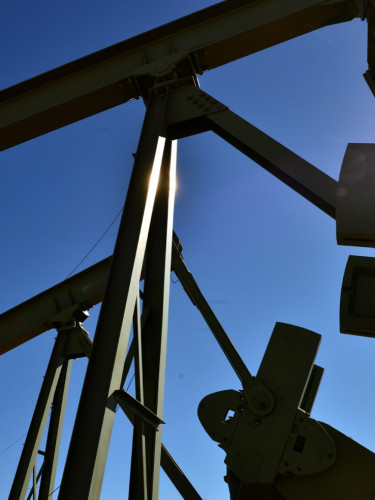
We find new resources, maximize production and responsibly develop areas previously thought unrecoverable.
ConocoPhillips is an independent exploration and production (E&P) company headquartered in Houston, Texas. We explore for, produce, transport and market crude oil, bitumen, natural gas, natural gas liquids and liquefied natural gas on a worldwide basis. Across geographies and geologies our commitment is the same: use our proven track record and expertise to safely and responsibly find and produce oil and gas.
ConocoPhillips has achieved notable success in unconventional reservoir exploration and development. We have developed, enhanced and employed advanced technologies such as time-lapse geochemistry, stimulated rock volume characterization, and interpretation of distributed acoustic and temperature-sensing measurements (DAS/DTS). Our technical staff extensively utilizes data analytics to optimize performance, enabling us to dramatically reduce drilling times, optimize production uptime, predict and maximize per-well resource recovery, and model environmental impacts.
We have significant positions in four of the six largest North American unconventional fields – the Permian, Eagle Ford, Bakken and Montney.
We optimize our world-class legacy conventional assets, including super-giant fields in Alaska and Norway, by deploying a combination of advanced proprietary and industry technology.
Our digital twins platform has enabled operators in Norway, Alaska and APLNG to navigate, plan and execute work more safely and efficiently. We are also working with technology startup companies to develop innovative ways of reducing the cost of plugging and abandoning mature fields, with these technologies gaining widespread acceptance globally. In Alaska, we are setting extended-reach drilling records that allow us to access resources that would otherwise be left behind, while reducing our surface footprint. Additionally, we operate several large enhanced oil recovery projects that employ innovative approaches to maximize hydrocarbon recovery.
ConocoPhillips has a 60-year history of leadership in liquefied natural gas (LNG) and was an industry pioneer in opening both the Atlantic and the Asia Pacific markets, as well as in developing the technologies needed to produce, transport and market this now-vital global resource.
Read more about LNG Technology and Licensing.
As global energy demand grows, Canada’s oil sands are emerging as one of the largest and most reliable long-term energy sources in the world. Surmont, located in the Athabasca region of northeastern Alberta and 100% owned and operated by ConocoPhillips, is a steam-assisted gravity drainage (SAGD) development that contains over a billion barrels of captured resources.
ConocoPhillips develops and applies technology in our oil sands projects to mitigate our impact on land, water and air, while optimizing oil production and improving economic returns. Since 2016, Surmont's GHG emissions intensity has declined by about 20%, and ConocoPhillips has plans for future operational emissions reduction by applying both current and new technology.
Energy is found all over the world, often in remote locations far from demand. We transport resources using tankers, trucks and rail, depending on the project, location, economics, accessibility and environmental considerations. All four methods are proven, efficient and economical ways of getting energy to market.
Pipelines
ConocoPhillips operates approximately 27,991 miles of oil, natural gas, liquefied petroleum gas and/or water pipelines throughout North America, the North Sea and the Asia Pacific region, including Australia. Onshore lines are located primarily in the Lower 48, Alaska and Indonesia, while offshore subsea pipelines are mostly in the North Sea (U.K. and Norway), Indonesia and China.
Tankers
In our North Slope operations, we manage marine transportation through our wholly owned subsidiary, Polar Tankers, Inc. Polar Tankers operates five Endeavour-class tankers in the Trans-Alaskan Pipeline System (TAPS) trade, loading crude oil in the Port of Valdez, Alaska, and delivering to terminals within Puget Sound, Washington, San Francisco and Los Angeles/Long Beach, California and Hawaii. For more information, visit Polar Tankers.
Tankers also transport natural gas, liquefied to reduce its volume significantly, from producers to consumers. A leader in the LNG business, we license our Optimized Cascade® process for liquefaction operations around the world.