“Here are the pumps,” said Senior Production Optimization Engineer Mike Lorenz, zooming in on the snapshot he captured from the 3D model. “Here are the valves. And here’s the check valve.”
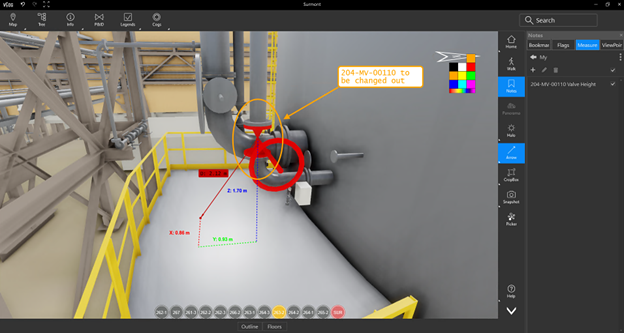
During a meeting with Surmont shift supervisors and maintenance personnel, Lorenz was using digital twin technology to show them where to isolate a pump for a potential hot-tapping job, a method of isolating a live pipeline for maintenance or repair without interrupting its flow.
Lorenz and other Surmont workers are using this visualization technology for various tasks, including site familiarization, conducting maintenance, locating equipment, planning work and taking measurements.
“I’m still learning about it,” Lorenz said of the digital tool, which functions like a documentation hub, putting detailed information at a user’s fingertips. “It’s very, very useful out here.”
Following the successful implementation of digital twins in Norway and Australia (APLNG), ConocoPhillips Canada has adopted this visual technology for use at Surmont’s Central Processing Facility 2 and Montney’s C-11-K central processing plant.
What is a digital twin?
A digital twin is a virtual replica — or “twin”— of a physical object that is connected to relevant data. It is a powerful tool that allows users to interact with a 3D version of field infrastructure and access engineering documentation from one user interface.
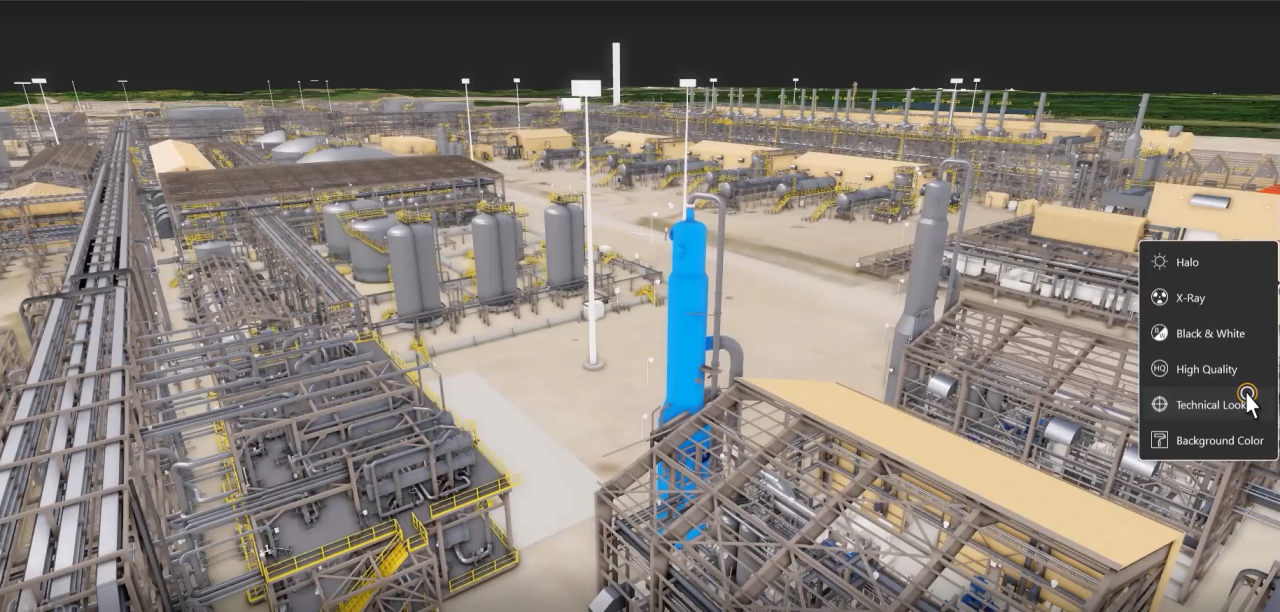
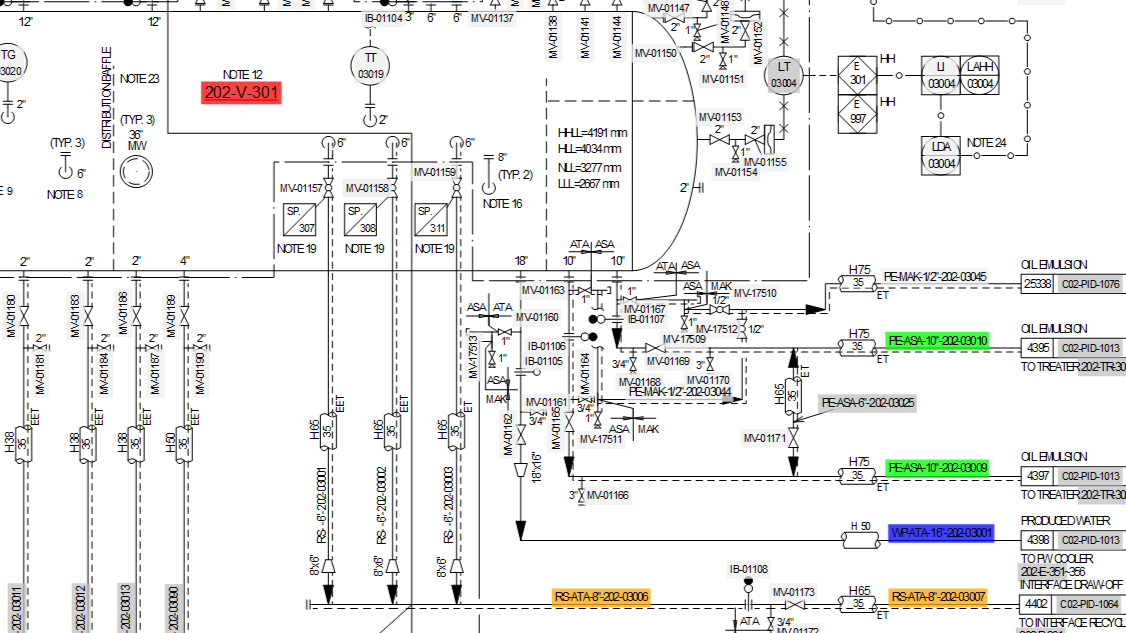
“I am confident our business will improve and become more efficient as we realize the benefits from this digital tool,” said Operations Support and Optimization Manager Rune Tufta, who is part of the leadership team involved in supporting the development and implementation of digital twins in Canada. “From my own experience in Norway and Australia, we have seen a lot of benefits by using digital twins, including more efficient planning and execution of work. The application will continue to mature to become even more powerful in the future. Bottom line, digital twins will help us improve our safety, cost, efficiency and production performance.”
Surmont Operations Manager Nicolai Lenning said workers are sharing how they are using the digital twin, reporting their experiences and providing feedback about the tool.
In one instance, Lenning said workers used the digital twin to locate a well-hidden spool, which is a prefabricated piece of pipe, for blinding. Blinding is the process of isolating a section of a pipeline to prevent the flow of fluids, allowing for safe maintenance or repairs. By using the virtual model, workers were able to precisely identify the location of the spool without the need for extensive physical searches or disruptions. This precise identification enabled them to isolate and blind the spool efficiently, preventing any unnecessary downtime or production halts.
In another case, workers used the digital twin for scaffold planning, streamlining the process.
“We can use the digital twin to enhance safety, effectiveness and precision in our planning and execution,” Lenning said.
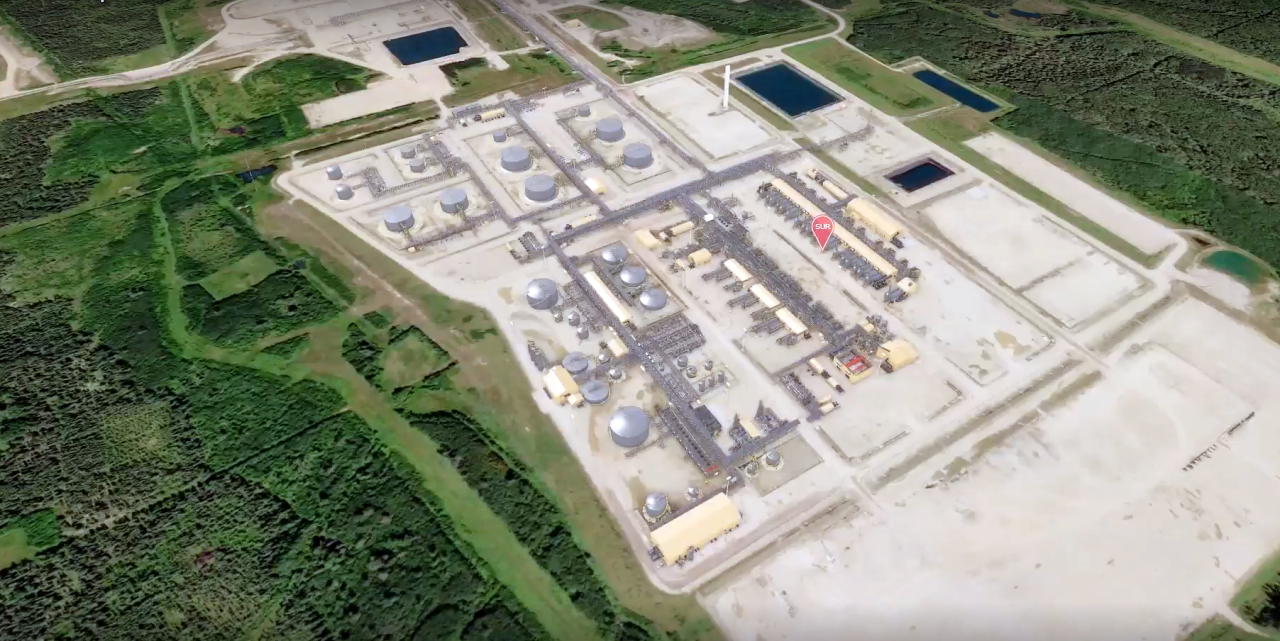
Turnaround Maintenance Coordinator Sean Lucas shared how personnel are leveraging the digital twin to optimize the planning process for turnarounds, which are scheduled maintenance events.
For simultaneous operations reviews, Lucas said planners can zoom in on the 3D model in the digital twin to see specific jobs at different elevations. “This makes it easier for us to assess risks and coordinate tasks,” he said, “which improves safety and productivity.”
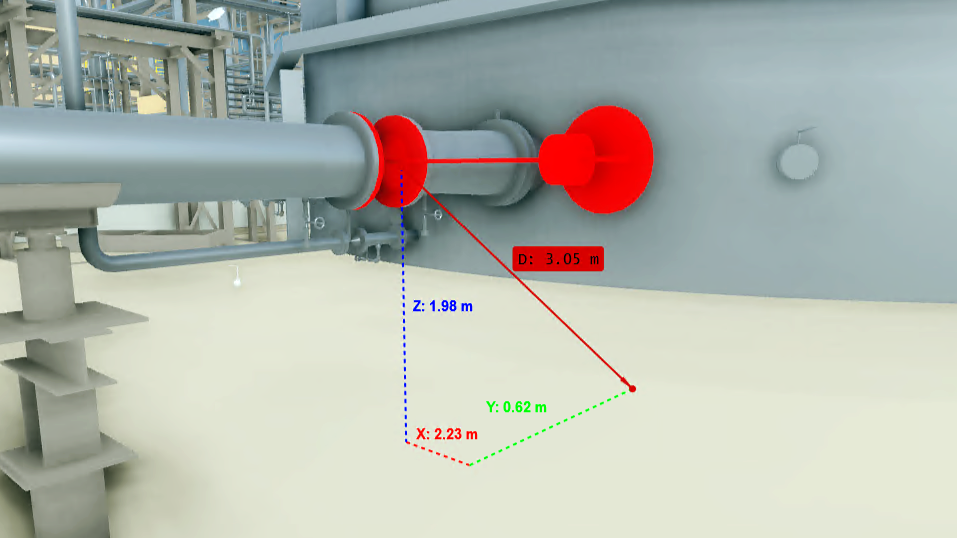
For detailed planning, Lucas said the digital twin gives workers precise job locations for work packs, which are documents that outline all the information, tasks and resources required to complete a job. “Soon, we’ll be able to search by location or work order,” he said, “which is a big upgrade from traditional 2D plot plans.”
In addition, workers are using the digital twin’s measurement feature to accurately gauge heights and distances for crane activities, ensuring the selection of appropriately sized cranes to avoid unnecessary costs.
“We are continually discovering new applications for its capabilities,” Lucas said.
Currently, the digital twin at Montney has limited functionality compared to Surmont. However, an upcoming content upgrade this summer will enhance the 3D model and improve data integration with SAP, documents and other sources.
Montney Operations Manager Tristan Howes said the technology packs a lot of potential.
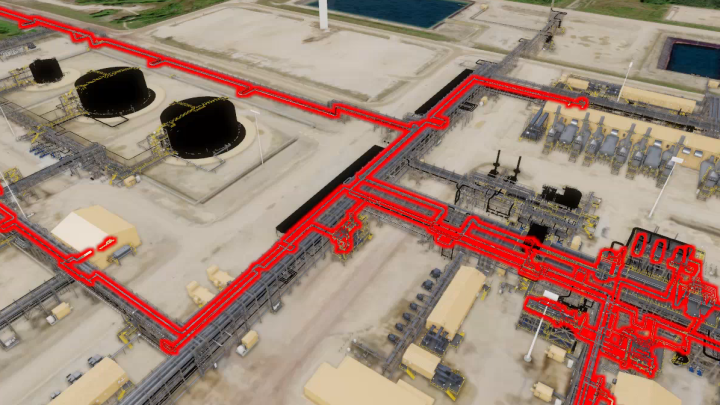
“Having firsthand experience at APLNG of seeing what the digital twin is capable of, I am looking forward to its continued integration within Montney and watching both the benefits and opportunities it opens for the workforce. We're just scratching the surface of what's possible.”
Data Science and Analytics Supervisor Michael Tenove manages the team responsible for the support strategy and processes for handling technical issues, content issues and future enhancements for Canada’s digital twins.
Tenove’s team has created a champion network to aid adoption. Power users within teams provide support and feedback, accelerating the technology's integration. ConocoPhillips’ Global Digital Twins team is also helping the Canada business unit with its implementation.
“Their support has been crucial for the successful rollout in Canada,” said Tenove, who estimated that it would take until the end of 2026 to fully build out the digital twins for the main facilities in Canada. “The ultimate goal is to create a comprehensive digital twin that serves as a central hub for information, integrating various data sources and enhancing operational efficiency over time.”
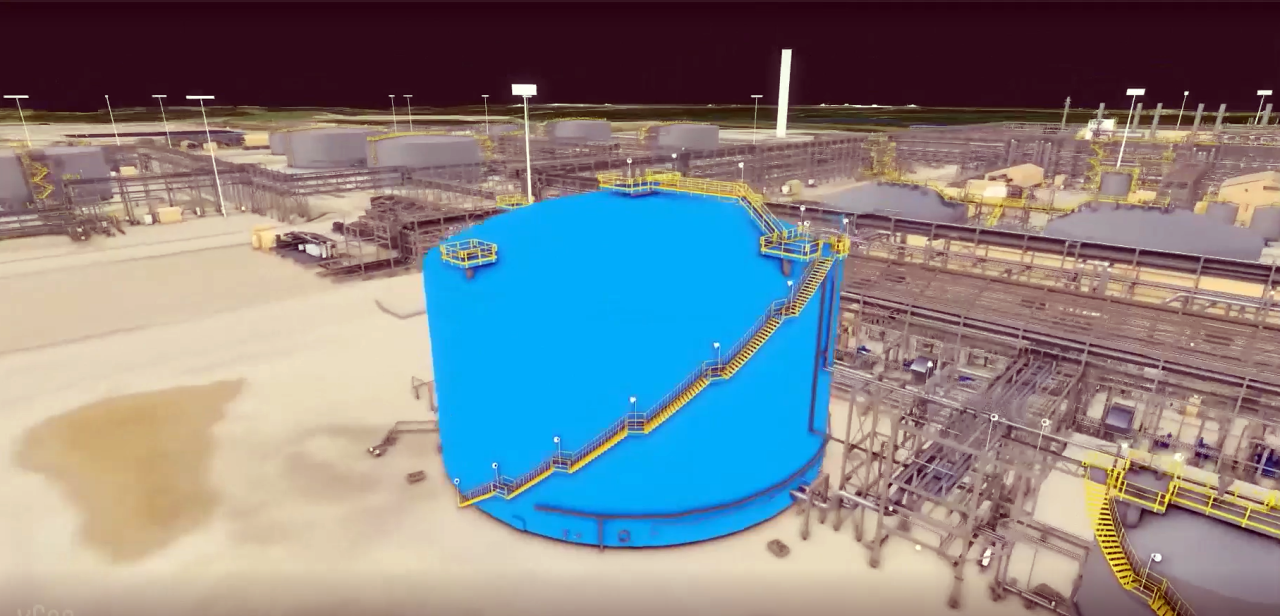