spiritnow Stories
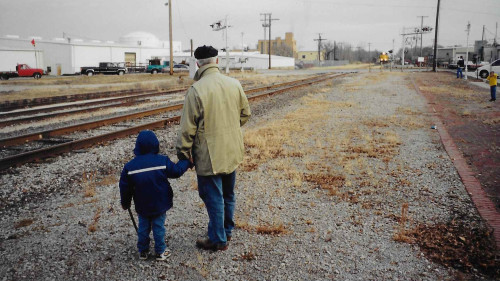
‘It’s what we do’ / Three generations of Gentrys deliver engineering excellence
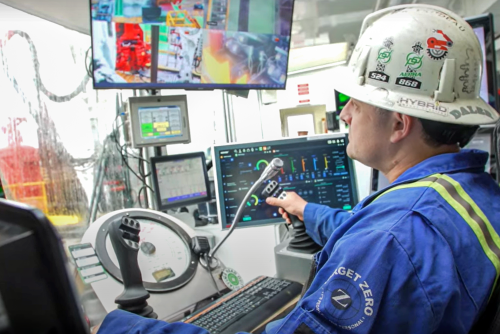
Enhancing safety and efficiency / Montney’s automated drilling rig
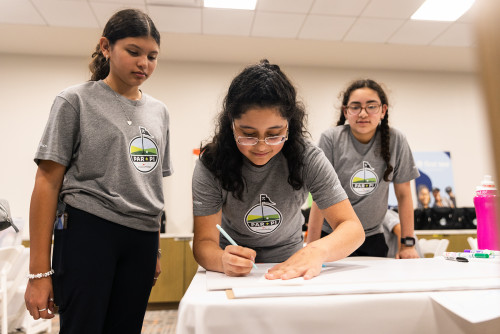
Par + Pi / New program teaches geometry through golf
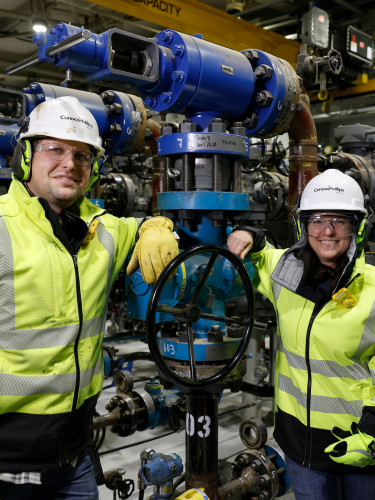
SPIRIT Values
The words are not proprietary to our company but the combination and the acronym are pure ConocoPhillips.
Swinging for the fences: Celebrating math teachers during baseball season
In April, Amber Sturdy, an Algebra teacher at Porter High School, was celebrated as Math Teacher of the Month and interviewed by sportscaster Robert Ford before an Astros game.
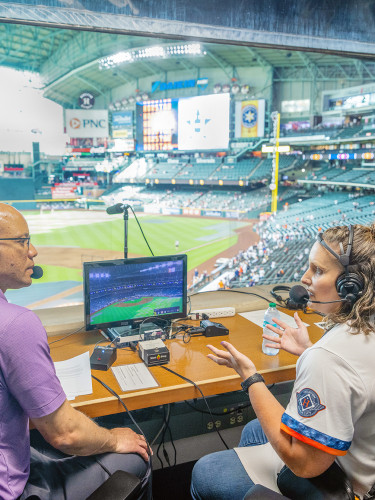