ConocoPhillips recently honored Lars Hovda with a 2023 Innovation Champion Award, recognizing his drive and commitment to the optimization of a well-plugging method extensively used by the company in the Greater Ekofisk Area.
Lars and his colleagues have optimized the Jet-type perforate, wash and cement (P/W/C) technique, which has enhanced efficiency when plugging wells in the Greater Ekofisk Area.
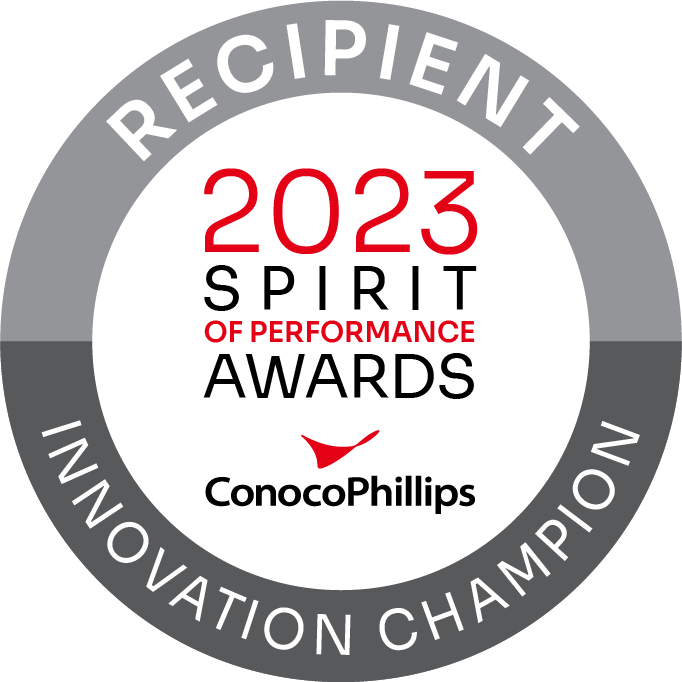
“It is great to receive this award on behalf of everyone who has worked on the project," Lars said. "Thanks to the fantastic colleagues who have contributed all these years.”
Lars, who joined ConocoPhillips 10 years ago, is an advisor for P&A engineering. He has extensive drilling experience, having worked onshore and offshore.
'A napkin sketch'
“We started exploring what we needed on a napkin sketch," Lars said. "The starting point for the thoughts was improving quality. It was really motivating that the senior drilling engineers at ConocoPhillips Norway and globally listened to us when we sparked the idea."
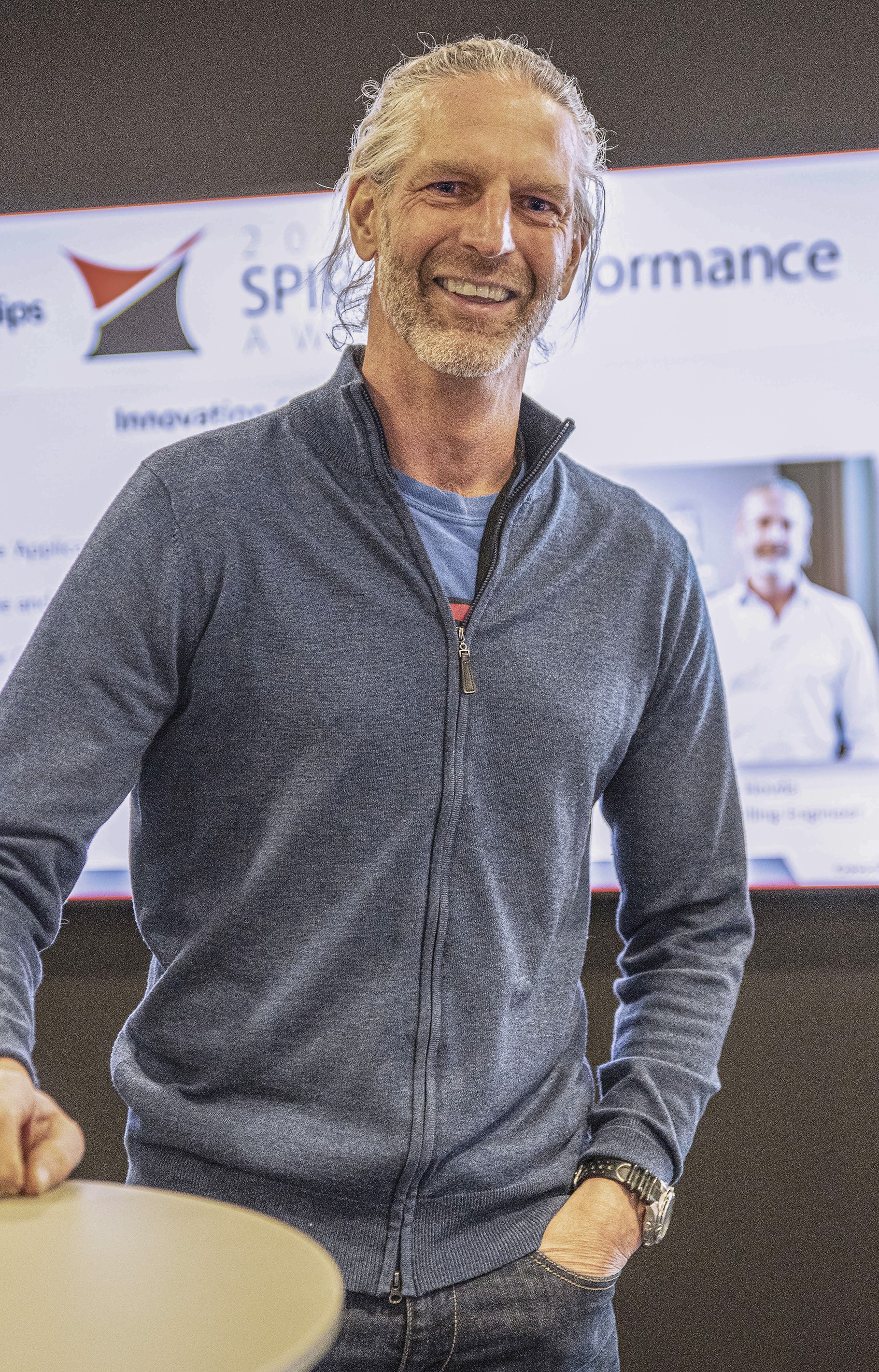
On a summer day in 2014, Lars and colleague Rick Watts were chatting after a meeting, discussing the challenges of P&A initiatives. P&A was an expensive undertaking and in the Greater Ekofisk Area most of the wells were old and prone to surprise issues.
It was difficult to develop a plugging technique that could be repeated according to the same procedure on each well.
In October of the same year, they presented an initiative at the 2014 PAF P&A conference, outlining what was needed to make the project fly.
“After this, we got input from suppliers," Lars said, "and the ball just started rolling."
The project group grew fast, and Lars started working with a cross-functional team from different parts of the world, experts who specialized in explosives, plugging materials, fluids and Computational Fluid Dynamics (CFD) software.
The initial optimized version of the P/W/C technique was introduced in 2015. By 2017, all parameters had been standardized and the optimization work was completed.
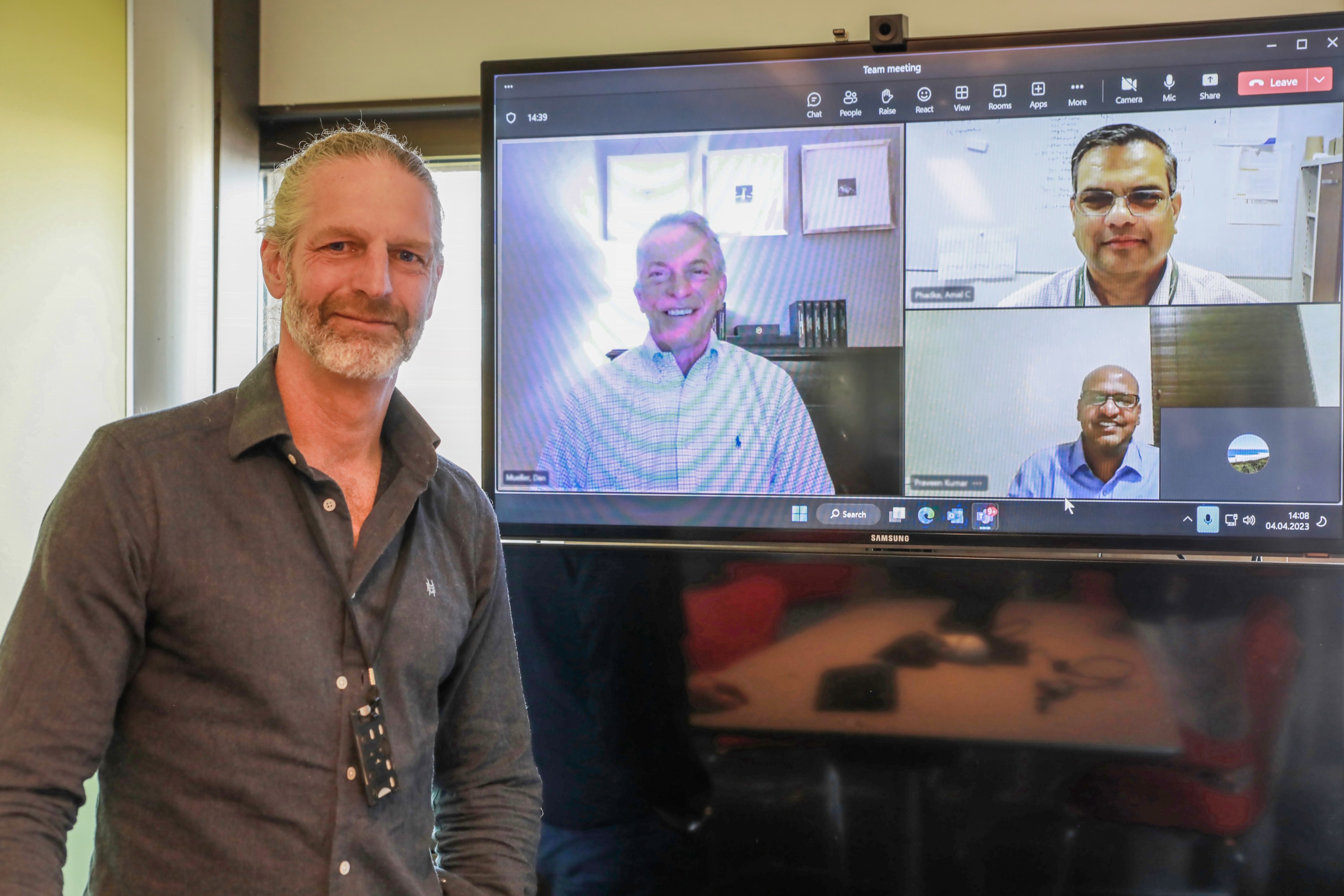
Improved performance when plugging wells
Since the standardization of parameters and completion of optimization, ConocoPhillips Norway has carried out 150 plugging operations using the Jet-type P/W/C technique in the Greater Ekofisk Area.
"This has led to significant rig time savings for the company," Lars said.
ConocoPhillips Norway's plugging activities are campaign-based. The business unit conducted P&A campaigns from 2014 to 2016 and from 2020 to 2022.
“Comparing the efficiency of these two periods is like night and day," he said. "We have improved the performance when plugging wells using this technique. In 2015, we were lucky if we managed to set a plug in 10 days. We have now reached the point where we can repeat operations, and budget two days on a plug. The way we are plugging using the P/W/C technique is reaching what we call a technical limit. This is about as good as it gets before a new technological breakthrough, a new napkin sketch."
Innovative plugging method
During the last 10 years, the Jet-type P/W/C technique has been extensively used in the Greater Ekofisk Area, becoming ConocoPhillips Norway's primary plugging method.
In P/W/C, tubing conveyed perforating (TCP) guns perforate the casing in the target interval before the zone is washed. Then a cross-sectional cement plug is installed using a specialized bottom hole assembly (BHA).
“TCP, BHA, drilling fluids and cement are existing technology," Lars said. "We have made some changes to this technology and put them together in a new way. The system has been tested and optimized in a CFD simulation software."
CFD has been used to maximize the cement plug's quality by optimizing the BHA and operational process parameters within the operating conditions' constraints.