KEY POINTS
- ConocoPhillips Norway receives 2024 SPIRIT Award for short-cycle subsea project execution.
- New strategy for marginal fields enables the use of standardized solutions across multiple projects.
- Team develops Tor II, Tommeliten A and Eldfisk North at approximately half the capital cost per produced barrel compared to traditional developments.
By Tore Falck
By adopting an innovative development strategy, ConocoPhillips Norway has significantly accelerated the transition of its subsea projects from the planning phase to first oil production.
Prioritized for optimization and efficiency, these North Sea projects exhibit characteristics akin to factory production, emphasizing standardization and reuse of previously proven technical solutions and execution strategies. Long-term contract strategies with suppliers have resulted in cost savings and reduced development expenses.
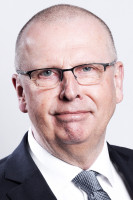
“We’ve become efficient and agile, focusing on the most critical tasks and seizing opportunities in collaboration with our suppliers,” said Europe and North Africa Capital Projects Manager Tor Inge Hansen. “We’re now ‘top quartile’ compared to international benchmarks of project management costs during project execution. That has been made possible by our dedicated team of world-class project professionals and highly committed vendors.”
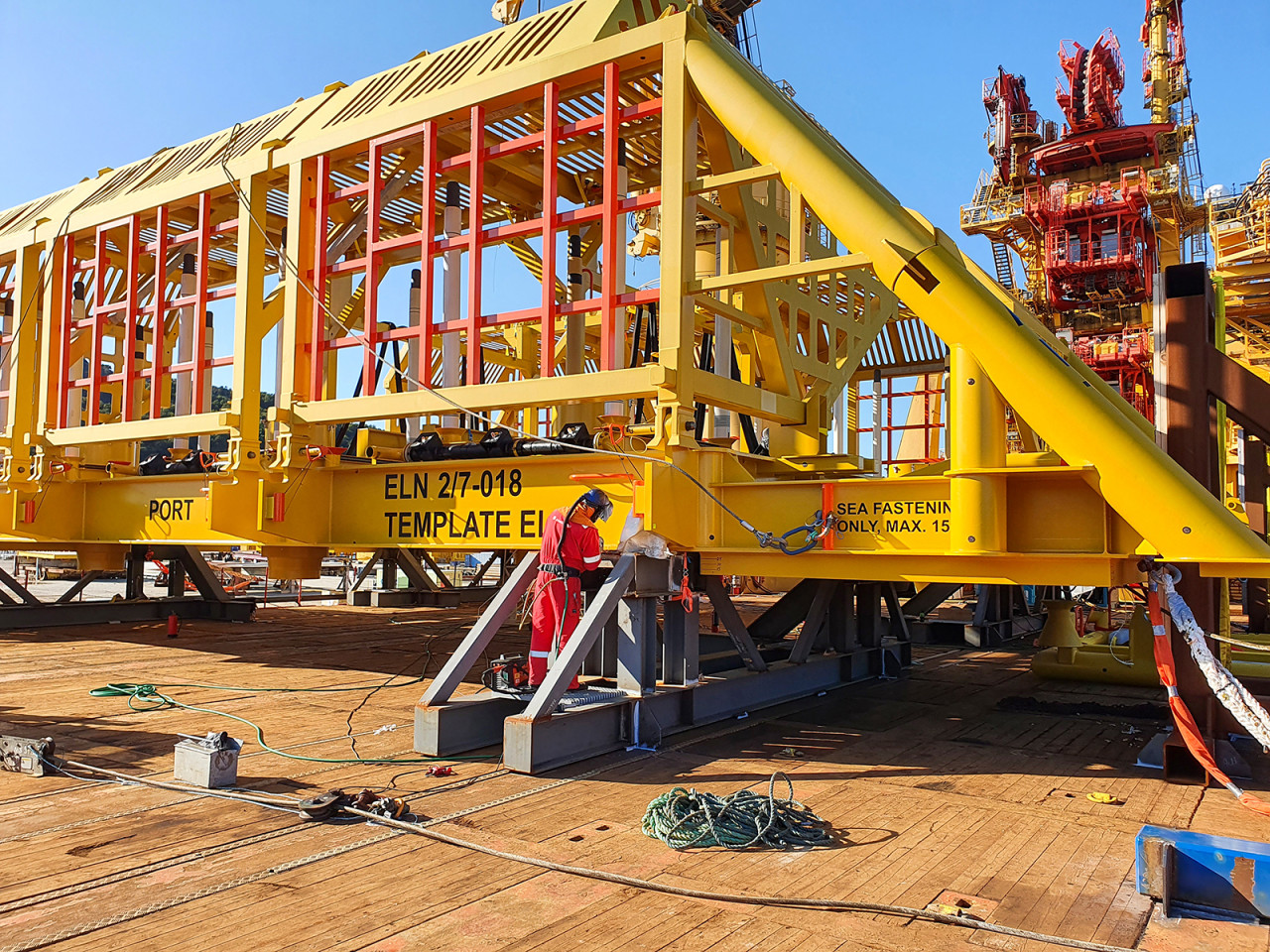
'We needed a new development approach for marginal fields'
ConocoPhillips had three development projects under consideration — Tor II, Tommeliten A and Eldfisk North — when oil prices declined in 2016. The concepts, based on fixed-bottom manned platforms with varying degrees of automation and remote control, would not have been profitable given the price outlook at the time.
“We had to think differently and find more cost-effective concepts,” Hansen said. “We needed a new development approach for marginal fields.”
The business unit explored the potential for unmanned installations. The ambition was to find an even better solution with more standardized products, allowing reuse of the approach across multiple developments with minimal extra effort.
"We succeeded in doing that through collaboration with suppliers and other operators," he said.
Our calculations showed that we could develop Tor II, Tommeliten A and Eldfisk North at approximately half the cost per produced barrel compared to traditional developments.
“Our calculations showed that we could develop Tor II, Tommeliten A and Eldfisk North at approximately half the cost per produced barrel compared to traditional developments,” Hansen said. “New subsea developments were made less time-consuming with earlier start-up of drilling activities, allowing us to deliver first oil sooner.”
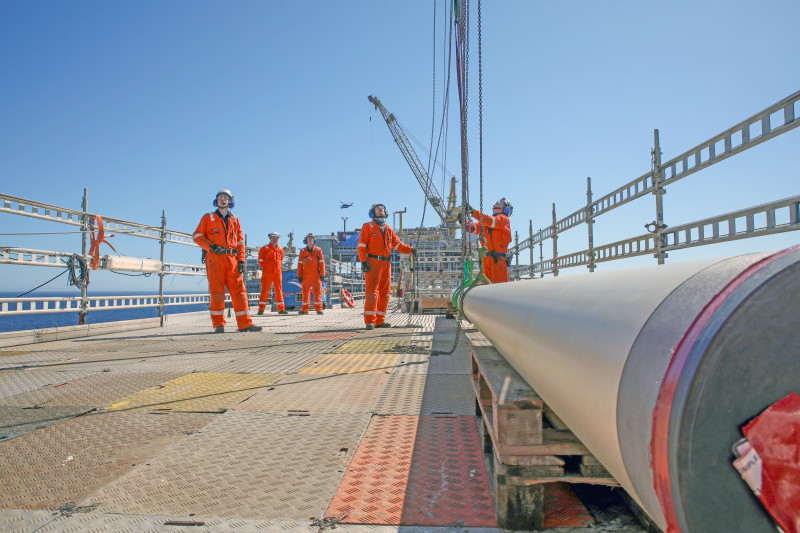
Reduced environmental footprint was also a top priority. The team sought creative ways to minimize emissions through more energy-friendly solutions. For example, the heated cable for the Tommeliten A pipeline — vital during startup, maintenance and end of field life — did not need to consume electricity continuously. Utilizing this approach improved both energy efficiency and reduced emissions.
“Similarly, we are considering more environmentally friendly control cables with electronic management to replace hydraulic systems," Hansen said. "Such initiatives help lower emissions. Leveraging existing processing and transportation infrastructure at all three projects allows us to reduce overall unit cost and lower emissions intensity by four to seven kilograms CO2 per barrel of oil equivalent."
The projects were executed safely and without significant incidents, despite workforce challenges during COVID-19, supply logistics issues, challenges following elevated security after the invasion of Ukraine, inflationary pressure and shortfalls throughout the supply chain.
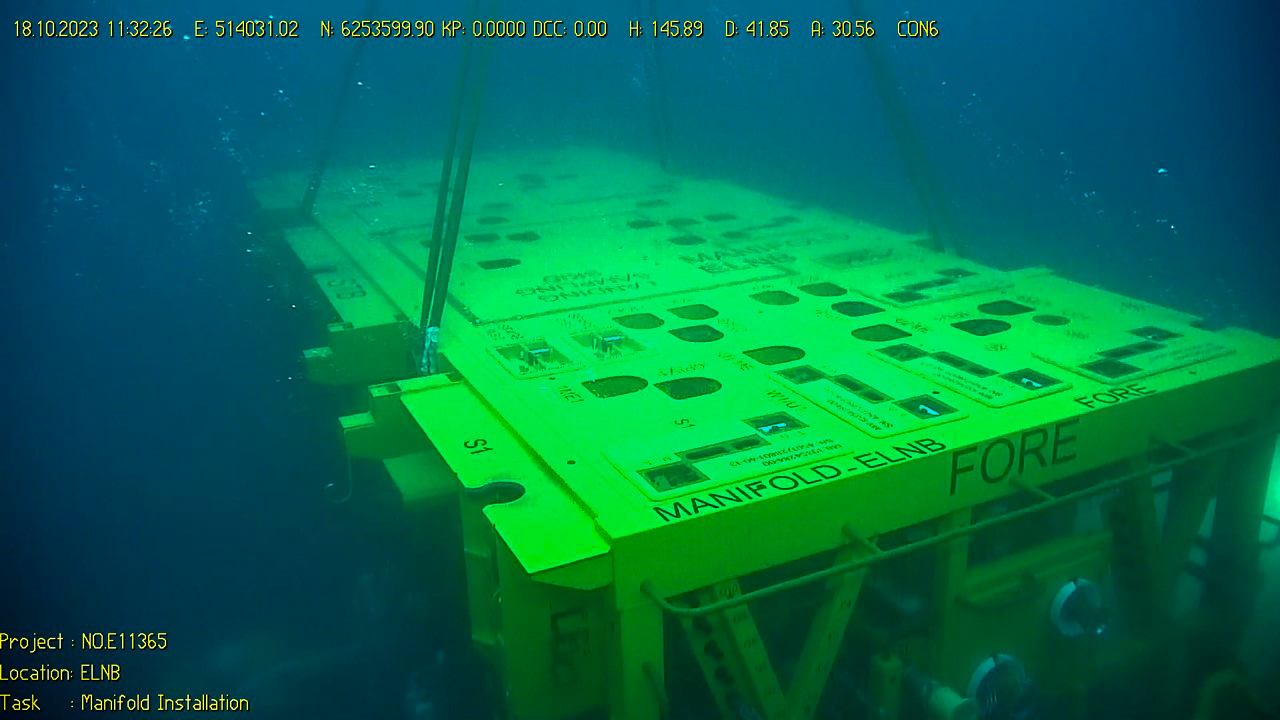
Collaboration and shared resources
An important premise for project execution based on this new development approach is strong collaboration with suppliers. By creating comprehensive framework contracts with two suppliers, ConocoPhillips has contributed to their success while ensuring healthy competition. If one supplier is underperforming, the company can choose the other supplier for the next project.
Given this palette of standardized solutions and long-term framework contracts, a large proportion of costs were agreed at very competitive rates in 2017. This paved the way for the three successive projects, ensuring benefits for all involved.
“As we gained more experience with these short-cycle developments, we recognized that stakeholders can gain significantly from more comprehensive agreements,” Hansen said. “For example, we’ve incorporated marine operations and equipment installation into contracts that previously covered limited deliveries. This enables us to engage fewer suppliers and streamline project management.”
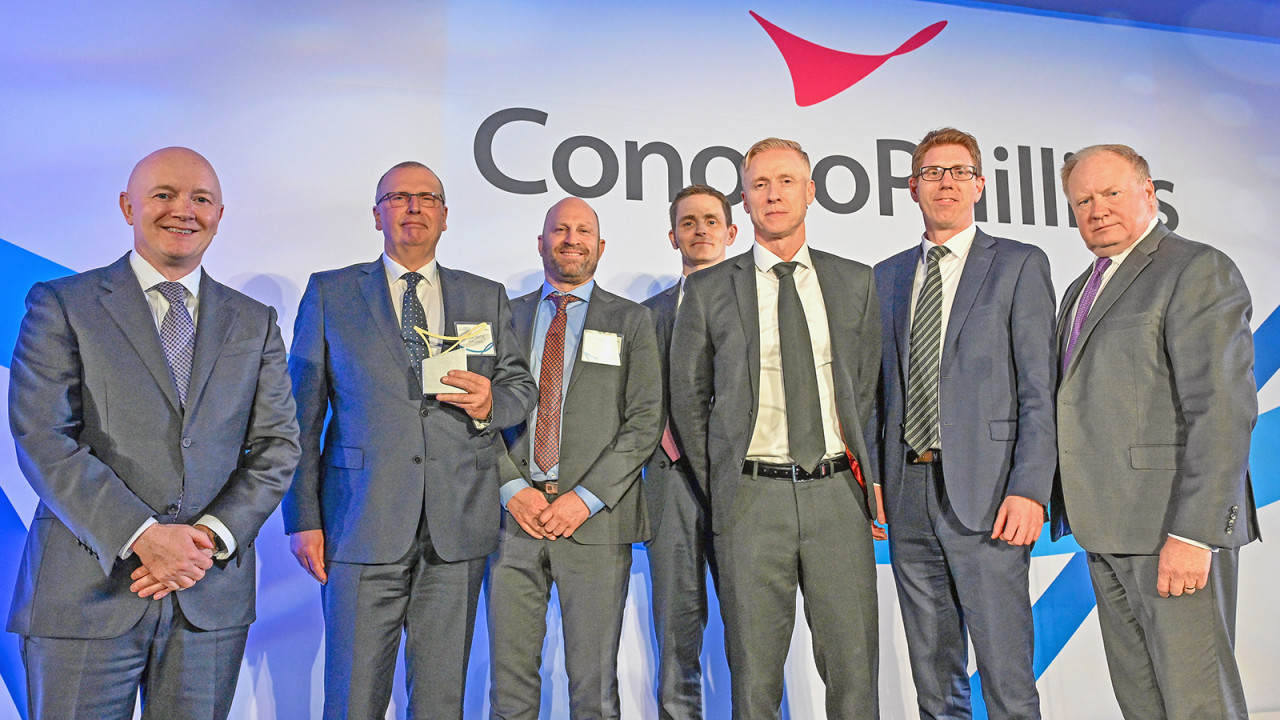
'We've proven their viability'
“Another prerequisite for success is continuously building our own competency,” Hansen said. “Prior subsurface and drilling knowledge gains must be integrated early into subsequent project plans."
Key players work together to mature projects within integrated project teams. Dedicated project integration managers coordinate support from various parts of the organization, ensuring clear responsibilities. A similar approach extends into the Operations organization for readiness to take over the project at first oil. Operational assurance managers are recruited early to ensure effective project handover.
“With this strategy and organization, we’ve achieved our goal to establish a development approach for marginal fields with lower capital cost and taking less time from start-up to handover," Hansen said. "We call these 'short-cycle projects,' and I think it’s safe to say we’ve proven their viability."